【倉庫作業】ピッキングの効率化とミスの削減方法をやさしく解説
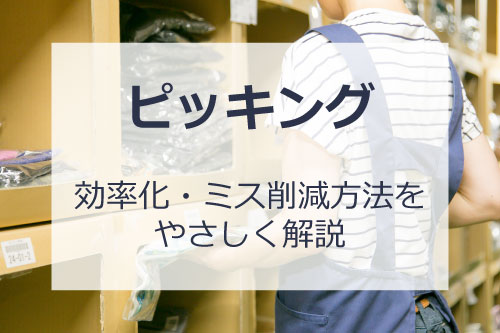
自社に物流部門を持つ企業であれば、倉庫作業において何かしらの課題を抱えていることが少なくないでしょう。特に、倉庫内の作業は多岐にわたり、その中で効率化が最も求められるのが「ピッキング作業」です。ピッキングは、商品の選定や出荷準備を行う重要な工程であり、作業効率や正確性が直接、物流全体のパフォーマンスやコストに影響を与えます。そのため、多くの企業がこの分野で課題を感じているのではないでしょうか。
本日は、倉庫作業の中でも特に多くの企業が改善の必要性を感じている「ピッキング作業」の効率化について詳しく解説いたします。この記事をお読みいただければ、ピッキングの基礎知識だけでなく、作業効率を向上させるための具体的な課題解決のポイントやヒントを得られるでしょう。
物流担当者の方々はもちろん、倉庫運営にかかわる管理職の方々や経営者の皆様も、ぜひこの記事をご覧いただき、倉庫作業の効率化に役立てていただければ幸いです。この記事を通じて、より効率的で無駄のない物流体制を実現する一助となることを目指しています。
目次
ピッキングとは
倉庫作業における「ピッキング」(英語:picking)とは、注文に基づいて必要な商品(在庫)を指定された数だけ棚から取り出す作業を指します。ピッキングは、商品の出荷準備において重要な工程であり、倉庫運営における効率化に直接的に影響を与えるため、非常に重要な役割を担っています。
英語の「pick」という言葉には、「摘む」「採集する」「選ぶ」といった意味がありますが、物流におけるピッキング作業は、単に商品を選び出すだけではなく、効率的かつ正確に作業を行うことが求められます。ピッキングが遅れたりミスが発生すると、配送遅延や誤配送につながり、結果として顧客満足度の低下や余分なコストの発生を招くことになります。そのため、ピッキング作業の効率化は、物流全体のコスト削減や顧客サービスの向上に直結する非常に重要な課題といえるでしょう。
特に、課題を抱えたままピッキング作業を続けると、無駄な人件費や時間が増加し、結果として全体の物流コストが上昇してしまいます。倉庫内で効率化を図るためには、ピッキングの作業フローを見直し、改善することが不可欠です。効率的なピッキング作業を実現することで、無駄な時間やコストの削減が可能となり、倉庫全体のパフォーマンスが向上します。
ピッキングの課題例
多くの企業はピッキングに対して、以下の課題を抱えています。
それぞれ解説します。
作業効率が悪い
たとえば、自社の倉庫で「商品がなかなか見つからない」という状況が発生していませんか? 特に在庫量が多い倉庫では、目的の商品を探し出すのに時間がかかり、作業効率が著しく低下することがしばしばあります。商品が多岐にわたり、さらに「カラー」や「サイズ」のバリエーションが豊富な場合、一度に多くの情報を処理しなければならず、時間がさらにかかるでしょう。
また、ようやく商品を見つけたとしても、次に「必要な数量」を正確にピッキングする作業が待っています。数が多いと、途中で数え間違えたり、いくつまで数えていたかが曖昧になってしまうことも少なくありません。このように、ピッキング作業が非効率だと、作業にかかる時間がどんどん増え、結果として全体の作業効率が大幅に低下してしまいます。さらに、時間の無駄が積み重なれば、物流コストの増加につながり、会社の利益にも悪影響を及ぼします。
ピッキング作業の効率化を進めるには、作業フローを見直し、商品配置の最適化や、適切なツールやシステムを導入することが必要です。例えば、ピッキングリストの電子化やバーコードスキャンの導入により、作業のスピードアップと正確性を向上させることができます。
ピッキングミスが発生している
ピッキング作業ではスピードが重要ですが、同時に「正確性」も欠かせません。しかし、実際の現場では商品の種類や数量を間違える「ピッキングミス」が頻繁に発生することがあります。このようなミスが発生すると、物流の効率化に支障をきたし、顧客にも大きな影響を与えます。
例えば、誤った商品を出荷してしまった場合、顧客に迷惑をかけるだけでなく、正しい商品を再送したり、返品を受け付けたりといった追加の対応が必要になります。これにより、再発送の送料や返品処理にかかる手間とコストが無駄に発生してしまい、結果として会社の利益が圧迫されることになります。また、顧客との信頼関係が損なわれるリスクもあるため、ミスを防ぐことは非常に重要です。
このようなミスを減らし、効率化を図るためには、ピッキング作業の自動化やシステムの導入が有効です。例えば、ピッキングアシストシステムや音声ガイダンスシステムを導入することで、作業員が正確に商品を選び出すことができ、ミスを大幅に減らすことが可能です。また、定期的な研修を通じて作業員のスキルを向上させることも、ピッキングミスの削減に効果的です。
ピッキング作業の効率化は、ミスを減らし、正確かつスムーズな物流運営を実現するための鍵となります。正確性とスピードを両立させることで、顧客満足度を向上させ、無駄なコストを削減することができます。
ピッキングの種類
まずはピッキングの基本的な知識として、「ピッキングの種類」について理解しておくことが重要です。ピッキングは、その運用方法によって主に以下の3種類に分類されます。それぞれの方式には、効率化に向けたメリットとデメリットが存在し、倉庫の特性やオペレーションに応じて最適な方法を選ぶことが肝心です。
では、それぞれのピッキング方法について詳しく解説します。
シングルオーダーピッキング
シングルオーダーピッキング(摘み取り方式)は、各注文ごとに商品をピッキングする方法です。1つの注文に対して、その注文で必要な商品だけをピッキングするため、間違った商品が混入するリスクを最低限に抑えることができます。この方式は、ピッキングの正確性を重視する場面で効果を発揮します。
しかし一方で、複数の注文に同じ品番が含まれている場合、同じ商品を何度も取りに行くことになるため、作業効率が低下する可能性があります。たとえば、品番Aが10件の注文に含まれている場合、各注文ごとにピッキング作業が発生し、10回もピッキングしなければなりません。
このように、ピッキング精度が高い分、効率性が欠けることもあるため、倉庫全体の作業効率を考慮した改善策が求められます。シングルオーダーピッキングを効率化するためには、商品の配置や移動の最適化が鍵となります。
トータルピッキング
トータルピッキング(種まき方式)とは、注文ごとではなく、必要な商品を一括でピッキングした後、注文単位に仕分ける方法です。この方式は、シングルオーダーピッキングとは異なり、同じ品番が複数の注文に含まれていても一度にまとめてピッキングできるため、ピッキング作業そのものの効率化が図れます。
さらに、トータルピッキングは、倉庫内での移動を最小限に抑えることができる点も大きなメリットです。商品をまとめてピッキングし、一筆書きのように効率的に倉庫内を移動することで、歩行距離を減らし、作業のスピードアップが期待できます。
ただし、この方式にはリスクも伴います。後で注文ごとに商品を仕分ける際にミスが発生する可能性があるのです。たとえば、注文Aの商品と注文Bの商品を混同してしまう「テレコ出荷」がその典型的な例です。このようなミスを防ぐためには、仕分け時の確認体制を強化することや、仕分け作業を支援するツールの導入が有効です。
※テレコ出荷については、以下の記事で詳しく解説しています。
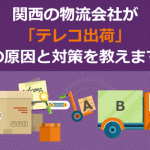
マルチオーダーピッキング
マルチオーダーピッキングとは、複数の注文を同時にピッキングしながら、ピッキングの途中でその場で仕分けを行う方法です。この方式では、ピッキングカートに複数の段ボール箱やオリコン(折りたたみ式コンテナ)を搭載し、各注文ごとに商品を仕分けながら作業を進めます。
マルチオーダーピッキングの大きな利点は、ピッキングと仕分け作業を同時に行うことで、効率化が図れる点です。トータルピッキングのように後から仕分けを行う必要がないため、作業のスピードが向上し、無駄な動きを減らすことができます。
しかし、同時に仕分けを行うため、商品の誤った組み合わせやミスが発生するリスクが依然として存在します。複数の注文を同時に処理するため、どの箱にどの商品を入れるべきかを常に正確に把握しておく必要があります。マルチオーダーピッキングの効率化を図るためには、作業員へのトレーニングの充実や、ピッキングカートや仕分けシステムの適切な利用が不可欠です。
各ピッキング方式には、それぞれの効率化に向けた課題と改善のポイントが存在します。自社の倉庫の特性や業務量に応じて、最適なピッキング方法を選び、効率化を進めることが重要です。
ピッキングを効率化するためのポイント
ここからは、ピッキング作業を効率化するために重要なポイントを2つご紹介します。これらの手法を取り入れることで、倉庫全体の効率化を図り、作業時間の短縮やミスの削減を実現できます。
ロケーション管理
倉庫内で必要な商品を迅速に見つけるためには、適切な「ロケーション管理」が不可欠です。ロケーション管理とは、倉庫内の「棚」に番号を付与し、その番号と商品を紐づけて管理する方法です。棚に付けられる番号は「ロケーションナンバー」と呼ばれ、これは商品の正確な保管場所を示す住所のような役割を果たします。
配達員が郵便物を届ける際に住所を頼りにするのと同様、倉庫内の作業員はロケーションナンバーを元にして商品を探し出します。このシステムが整備されていることで、目的の商品を素早くピッキングすることが可能になり、作業効率が大幅に向上します。特に商品数が多い大規模な倉庫においては、ロケーション管理がしっかりしているかどうかが、ピッキングのスピードと効率に直結します。
また、ロケーション管理の精度を上げるためには、定期的な棚卸しや在庫の整理も重要です。棚卸しを効率化することで、常に正確な在庫情報を把握でき、無駄な探し作業を減らすことができます。これにより、ピッキング作業全体の効率化が促進され、倉庫運営がスムーズになります。
ABC分析
「ABC分析」は、倉庫内の商品を出荷頻度に基づいて3つのカテゴリーに分類し、効率的に管理するための手法です。この分析を通じて、倉庫内のレイアウトを最適化し、ピッキング作業を効率化することができます。以下は、ABC分析の基本的な考え方です。
ABC分析を行うことで、最も頻繁に出荷される「A商品」を倉庫内で最もアクセスしやすい場所に配置することができます。具体的には、ピッキング作業の動線上、最短でアクセスできる場所や、目線の高さに近い棚に配置することで、ピッキングにかかる時間を大幅に短縮できます。逆に、「C商品」は出荷頻度が低いため、倉庫内の奥まった場所や高い位置に配置し、倉庫スペースを効率的に使うことができます。
このように、出荷頻度に基づいて商品を配置することで、倉庫内の動線が最適化され、作業員の歩行距離が短縮されます。結果として、ピッキングの効率化が進み、全体の作業スピードが向上します。さらに、ABC分析は倉庫のレイアウト変更や在庫の適正化にも役立ち、季節やトレンドに応じて商品の配置を柔軟に調整することで、さらなる効率化が図れます。
以上のポイントを実践することで、ピッキング作業だけでなく、倉庫全体の効率化が進みます。ロケーション管理とABC分析を組み合わせて取り入れることで、無駄を減らし、最適な倉庫運営を実現しましょう。
ABC分析については、以下の記事で詳しく解説しています。
ピッキングのミスを削減する方法
ピッキング作業におけるミスを削減するためには、倉庫の効率化に直結する管理システムであるWMS(Warehouse Management System)の導入が不可欠です。WMSは、在庫管理や作業の効率化を実現するだけでなく、ピッキングミスを防ぐための重要な役割を果たします。
具体的には、まずピッキングリスト(出荷指示書)に添付されているバーコードを、作業員がハンディーターミナル(業務端末)でスキャンします。この作業により、ピッキングすべき商品の情報がWMS上に正確に反映され、次のステップに進む準備が整います。
次に、ピッキングリストに記載されたロケーションナンバーを参照し、倉庫内で商品が保管されている棚まで移動します。ロケーション管理が徹底されている場合、このナンバーによって作業員は迅速に正しい場所にたどり着けます。続いて、目的の商品を棚からピッキングし、商品に添付されているバーコードを再度スキャンします。
この一連の作業を通じて、WMSはピッキングリストのデータと商品のデータをリアルタイムで照合し、ピッキング内容に誤りがないかをチェックします。これにより、ミスを未然に防ぐことができるのです。もし誤った商品をピッキングしてしまった場合でも、WMSが即座にエラーを検知し、作業員に修正を促します。
ピッキングミスを減らすためには、作業員に依存するのではなく、システムに判断を任せることが重要です。というのも、ピッキングミスの多くはヒューマンエラーによるものであり、複雑な作業や時間のプレッシャーが原因で発生することがほとんどです。人が判断する部分を減らし、WMSに自動的に誤りを検出させることで、倉庫作業の効率化を図るとともに、ピッキングミスを大幅に削減することが可能になります。
さらに、WMSの導入によって、倉庫全体の作業が可視化され、在庫の正確な把握や作業の進捗状況のモニタリングも簡単になります。これにより、効率化が一層進み、作業の精度が向上します。ピッキングミスをなくすことは、結果的に無駄な再配送や返品対応の削減にもつながり、物流全体のコスト削減にも寄与します。
倉庫内でのミス削減を目指すなら、WMSの導入を検討し、作業フロー全体を効率化することが不可欠です。
WMSについては、以下の記事で詳しく解説しています。
おすすめはクラウドWMS「BEELOGI(ビーロジ)」
ここでは、倉庫の効率化を支援するおすすめのWMSをご紹介します。
クラウドWMS「BEELOGI(ビーロジ)」は、物流業界で29年以上の実績を持つ弊社トミーズコーポレーションが提供するサービスです。このシステムは、スマートフォンをハンディーターミナルとして活用することにより、低コストでの運用を実現しています。従来の専用端末を使用するWMSに比べ、導入コストが抑えられるため、初めてWMSを導入する企業様でも手軽に取り組むことが可能です。
「BEELOGI(ビーロジ)」は、ピッキング作業の効率化に特化しており、作業時間を短縮しながらミスを大幅に削減することができます。ロケーション管理やバーコードスキャン機能を駆使して、ピッキングの精度を向上させ、無駄な移動や探す手間を省くことができるため、倉庫作業全体の効率が飛躍的に向上します。特に、ヒューマンエラーの削減に大きな効果を発揮し、倉庫内のオペレーションをよりスムーズに進めることが可能です。
さらに、「BEELOGI(ビーロジ)」はクラウドベースのシステムであるため、いつでもどこでもアクセス可能で、複数拠点を持つ企業でも容易に全体の在庫やピッキング状況をリアルタイムで管理することができます。この柔軟性により、倉庫運営の効率化が進み、企業の物流戦略をより強力にサポートします。
手前味噌ではありますが、ピッキングの効率化やミスの削減を実現するためには、「BEELOGI(ビーロジ)」は非常に有効な手段と言えるでしょう。また、無料トライアルも実施しておりますので、まずはお気軽にお試しいただき、その効果を実感してみてください。倉庫作業の効率化を図りたい企業様にとって、最適なソリューションになること間違いありません。どうぞお気軽にお問い合わせください。
まとめ
この記事では、倉庫作業におけるピッキングの基礎知識に加え、ピッキング作業の効率化に向けた課題解決のポイントについて詳しく解説しました。ピッキングの効率を向上させるためには、ロケーション管理やABC分析といった基本的な手法の導入が鍵となり、さらにWMS(倉庫管理システム)の活用によって、作業の精度とスピードを同時に向上させることが可能です。
自社の物流業務でピッキング作業に課題を感じている方や、倉庫全体の効率化を目指している方は、ぜひ本記事の内容を参考にして、改善策を取り入れてみてください。ピッキング作業の改善は、倉庫内の無駄を削減し、物流コストの削減や顧客満足度の向上につながる重要なステップです。倉庫業務の効率化に取り組むことで、さらなる成長と競争力の向上を目指しましょう。
クラウドWMS「BEELOGI(ビーロジ)」の無料トライアルはこちら
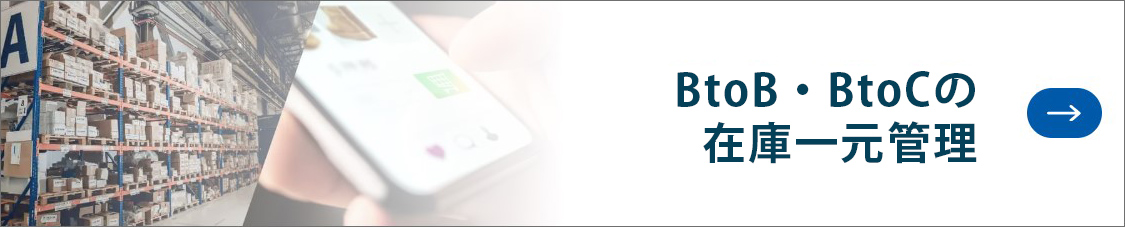