倉庫レイアウト改善の考え方!最適化する方法を解説
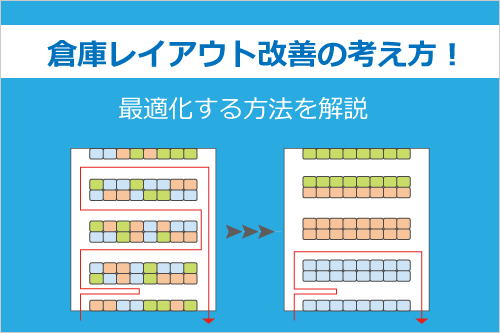
「倉庫スタッフの人件費」や「商品を出荷するまでの時間」に課題を抱えていませんか?
物流倉庫の課題は、「レイアウト」を見直せば、改善できる場合があります。
そこで今回は、倉庫のレイアウトの改善方法を図解でわかりやすく解説。
この記事を読めば、自社の倉庫作業を効率化できます。
目次
倉庫レイアウトとは
倉庫レイアウトとは、商品の「保管場所(配置)」や「保管方法」を決めること。
では一体なぜ、倉庫レイアウトを改善しなければいけないのでしょうか?
次に解説します。
倉庫レイアウトを改善するメリット
倉庫レイアウトを改善するメリットは、主に以下の3つです。
それぞれ詳しく解説します。
物流コストを削減できる
倉庫作業には、主に以下の工程があります。
これら倉庫作業の工程のなかには、少なからず「ムダ」が潜んでいます。
たとえば、「ピッキングに時間がかかっている」という場合は、倉庫スタッフの「動き」にムダがある可能性があります。倉庫スタッフがスムーズに作業できるように改善すれば、人件費を削減できます。
その他、「倉庫に商品が入りきらない」という場合は、「保管効率」が悪い可能性があります。保管効率を上げれば、1商品あたりのコストの削減が可能。また、倉庫の拡充を見送ったり、遅らせたりもできます。
出荷リードタイムを短縮できる
出荷リードタイムは、注文(出荷指示)を受けてから、商品を出荷するまでに要する時間です。
倉庫作業のムダを徹底的に省けば、効率化できるため、出荷リードタイムを短縮できます。
たとえば、1日の出荷量が100件、1商品あたりのピッキング平均時間が5分だと仮定。1分短縮できれば、合計100分(1時間20分)の削減につながります。
100分余れば、追加25件(=100分÷4分)を出荷できますよね。本来、翌日出荷分であった25件については、出荷リードタイムを削減できることになります。
お客様になかには、商品が手元に届くまでの日数を確認してから注文する方もいるでしょう。出荷リードタイムを1日でも短縮できれば、今後の売上を拡大できます。
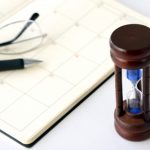
ミスや事故を減らせる
倉庫作業にミスが発生してしまうと、お客様に迷惑がかかります。一度失った信頼はなかなか取り戻せません。
また、レビューやクチコミなどに、悪評が書き込まれてしまった場合は、今後の売上にも影響がでます。
さらに重要なのは安全です。事故があれば従業員にケガを負わせてしまいます。最悪の場合、行政指導により「営業停止処分」を受ける可能性も。
日々の倉庫運営は、「安全の上に成り立っている」と考え、第一優先に取り組みましょう。
倉庫レイアウトを改善するための準備
倉庫レイアウトを改善するとき、まず現状の課題を抽出しましょう。
課題を見つけるポイントは、さきほど解説した「倉庫レイアウトを改善するメリット」と同じ内容です。
主に、「倉庫作業にムダが発生していないか」や「ミスや事故につながる要因はないか」などを洗い出します。
とくに、安全面は重要。国土交通省が「倉庫管理主任者マニュアル」を公表しているので、参考にしてください。
倉庫レイアウト改善の手順
それでは、倉庫のレイアウトを改善する手順を解説していきます。
主な手順は、以下のとおりです。
手順1.基本のレイアウト「I型」と「U型」から選ぶ
倉庫レイアウトの理想は、一筆書きの導線にすること。
倉庫における導線とは、人・物が移動する経路を指し、作業を効率化するのに重要な役割を担います。
一筆書きの導線であれば、倉庫内を行ったり来たりせずに済みます。入荷から出荷までの倉庫作業の流れをスムーズにできるでしょう。
ここでは、一筆書きの導線としておすすめできる「I型」と「U型」の倉庫レイアウトを解説します。
I型の倉庫レイアウト
I型の倉庫レイアウトは、入口で入荷検品、出口で出荷検品をするため、商品が混合する心配がありません。
またI字型は、商品を直線的に配置するため、デッドスペースが少なく、狭い倉庫でもしっかりと在庫数を確保できるのがメリット。
ただし、入口と出口が対面に無いなど、倉庫の構造上、I型の倉庫レイアウトを選べない場合は、U型がおすすめです。
U型の倉庫レイアウト
U型の倉庫レイアウトなら、出入り口が一つしかない倉庫にも適用可能。
出入口付近に「入荷検品」と「出荷検品」それぞれ専用のエリア、奥に「ピッキングエリア(保管スペース)」を設けます。
手順2.出荷頻度別のABC分析をする
基本のレイアウトが決まったら、次にピッキング効率や保管効率を上げる目的で、「出荷頻度別のABC分析」を行います。
過去の出荷実績データをもとに、商品を以下のABCに分類しましょう。
商品の分類作業には、「パレートの法則」を知っておくと便利です。
パレートの法則とは、 「全体の成果の8割は、全体の2割の要素で構成される」といった傾向。※別名「2:8の法則(ニッパチの法則)」とも呼ばれます。
つまり、出荷頻度の高い上位2割を「A商品」とすればよいのです。
ただし、単に出荷頻度だけで判断すると、シーズン性やセールなどの要因を考慮できません。倉庫レイアウトの改善は、あくまでも今後を見据えて取り組む必要があります。
たとえば、9月に倉庫レイアウトの改善を行う場合、直近3ヶ月、つまり夏の出荷実績データを取得しても効果的ではありません。夏に売れたものが、秋も売れるとは限らないためです。
出荷実績データを参考としながらも、自社商品の特性を考慮したうえで、分類しましょう。
手順3.「A」は最短の導線となるように配置する
以下、I型レイアウトもU型レイアウトも共通して、出荷頻度別のABC分析で「A」に分類した商品は、最短の導線となるように配置します。
I型レイアウトの「A」の改善例
「A」に分類した商品は、通路側に配置すれば、商品をピッキングするときの「歩く距離」を減らせます。
U型レイアウトの「A」の改善例
「A」に分類した商品は、入口付近に配置すれば、商品をピッキングするときの「歩く距離」を減らせます。
手順4.「C」は保管効率を重視して、パレット保管を併用する
出荷頻度別のABC分析で「C」に分類した商品は、出口から一番遠い場所に保管します。
また1商品(品番)あたりの在庫量を減らし、商品数(品番数)を増やします。
棚を細かく仕切れば、通常より多くの商品数(品番数)を保管できます。
さらに「C」商品のストック分は、ケースに入れてパレットで保管(ケース保管)しましょう。
ネステナーなどで高積みすれば、保管効率が上がります。
倉庫レイアウト安全面の注意点
倉庫レイアウトを決定する前に、「安全に考慮されているか」を入念に確認しましょう。
ここでは、倉庫レイアウトを決定するときに、安全面から注意していただきたい点を解説します。
通路幅を確保する
I型レイアウトやU形レイアウトは一筆書きの導線。しかし、「通過した道を戻らないか」というと、必ずしもそうとは言い切れません。ピッキング漏れなどが原因で、後戻りすることもあるでしょう。
そのため、最低限人と人がぶつからない程度の通路幅は確保すべきです。
フォークリフトを使用する場合は、フォークリフト2台分の通路幅を設けましょう。フォークリフト1台しか通れない通路幅では、はちあわせた際にどちらかが後退しなければなりません。作業効率が落ちるのはもちろん、事故にもつながります。
ラインテープを貼る
導線を明確化するために、ラインテープを貼りましょう。
以下、黄色い線がラインテープ。市販されているので、すぐに手に入ります。
通路に商品が置かれていると、人がぶつかってしまう可能性があり、事故につながります。
ラインテープを貼ると、倉庫スタッフが、「通路に商品を置いてはいけない」という意識を持てたり、通路に飛び出した商品があればすぐに気づけたりします。
ラインテープは、通路幅を確保するために重要な役割を担うのです。
倉庫レイアウトの改善はプロに依頼できる
倉庫レイアウトの改善はプロに依頼できます。
できれば、物流コンサルティングなどの実績がある会社が良いでしょう。
最適な倉庫レイアウトは、企業ごとに異なります。商品の特性や出荷形態など、ありとあらゆる側面からベストなレイアウトを導き出さなければなりません。
まとめ
この記事では、倉庫レイアウトの改善方法を、図解を用いて解説しました。
弊社トミーズコーポレーションは、物流25年を超える発送代行会社です。物流コンサルティングサービスも提供しており、お客様に最適な倉庫レイアウトをご提案できます。
お客様事例も掲載しておりますので、興味のある方はご覧ください。
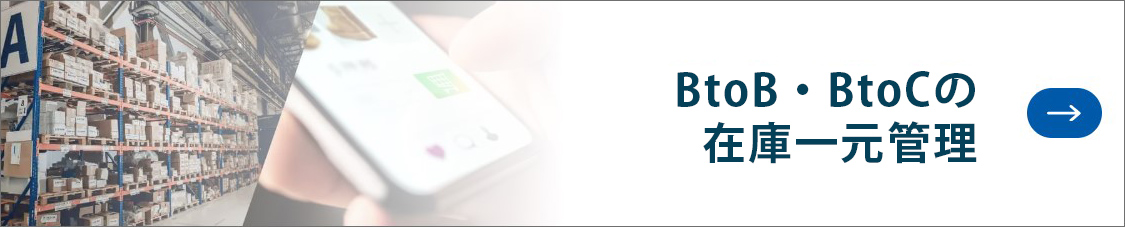