物流改善で「歩かない」が浸透している理由
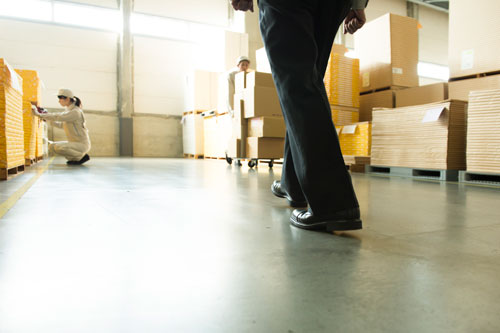
一見、物流現場で「歩かない」と聞くと「仕事にならないのでは?」と感じてしまうかもしれませんが、物流改善におけるコスト削減という意味ではこの「歩かない」という考え方が浸透しています。本日はその「歩かない」について少し詳しく説明いたします。
目次
歩行時間と生産性
歩かないとは「歩行時間」を短くするということです。歩行時間が長ければ倉庫作業における生産性を落とす結果を招いてしまいます。1つの商品をピッキングするのに1分かかっている作業と30秒しかかからない作業では、前者の作業は生産性が2倍かかってしまうことになります。「30秒しか変わらないのでは?」と思われた方も少なくないはずです。それでは具体例を上げてみます。
例えば、商品を100個ピッキングするとします。前者は作業時間が100分かかるのに対して、後者は50分で済みます。これが1000個になれば500分、つまりは8時間以上の差が生まれてしまうことになります。「塵も積もれば山となる」ということわざがあるように、この1作業30秒の違いでも、作業数が多く、またそれが毎日続くとなると結果的に大きな違いが生まれることになります。つまりは歩行距離(=歩行時間)を短くすることができれば生産性も上がることから、物流改善ではこの「歩かない」が非常に重要な意味を持つことになります。
「歩かない」ための工夫
エリア間の歩行時間
物流倉庫では入荷エリアや保管エリア、出荷エリアと色々なエリアを分けて作業されることがありますが、一人の担当者でそれらエリアをまたいで作業する場合は、そのエリア間の移動時間がその都度必要になるため、非効率になる場合があります。移動時間は実際に作業していない時間となる為、生産性を落とす要因になりかねません。そのため、エリア間に長い距離が存在する場合、エリアごとに担当者を配置した方が生産性が上がる場合があります。例えば、入荷であれば入荷エリアに入荷検品担当者を配置し、保管エリアには入庫担当者を配置します。また、出荷であれば、エリア毎のピッキングを行い、リレー方式で出荷先毎の商品を合わせます。
エリア内の歩行時間
作業エリアが広く、出荷頻度が高い商品があちらこちらに散らばっていては歩行距離が増えてしまうため、生産性が落ちてしまいます。そのため、商品ABC分析により出荷頻度に応じたロケ管理を行うことが大切です。出荷頻度の高い商品をなるべく狭いエリアに集中させることで歩行距離を短くすることが可能になります。ただし、注意点があります。出荷頻度の高いものを狭いエリアに集中しすぎてしまうと、渋滞を招き、結果的に生産性が低下する可能性があります。そのため、歩行距離を意識しながらも渋滞しないように適度に分散させることも重要です。
ピッキング方式の選定
出荷数が多い物流倉庫ではピッキング作業がもっとも大きな作業工数になる場合があります。そのため、シングルオーダーピッキングやトータルピッキング、マルチオーダーピッキングといった、ありとあらゆるピッキング方法の中から、出荷先毎に最適なピッキング方法を取拾選択し、場合によっては複数のピッキング方法を駆使して作業する必要があります。(ピッキングの種類については以前の記事をご覧ください。)
WMSの導入
WMSと呼ばれる倉庫管理システムは倉庫管理に特化したシステムとなっているため、ピッキング作業を効率化するための仕組みが備わっている場合があります。例えば、ピッキングリストの出力では、目的に合わせた順番に切り替えてピッキングリストを出力する機能があります。注文順や品番順といった基本はもちろんのこと、SKU数の少ない注文順に出力できる機能や、ロケーション順に出力できる機能等があります。これらを使用することでベストなピッキング作業を実現することができます。
いかがでしたでしょうか?
トミーズコーポレーションでは「歩かない」ための物流オペレーションを構築しております。
そのために必要不可欠なのがWMSと呼ばれる倉庫管理システムの導入です。
トミーズコーポレーションではクラウドWMS「ビーロジ」をサービス提供しております。
ピッキング作業効率を最大限高められるように考えられたシステムですので、ご興味ある方はまずは一度お気軽にお問い合わせくださいませ。
効率的なピッキングを実現したい方はクラウドWMS「ビーロジ」がおすすめです。
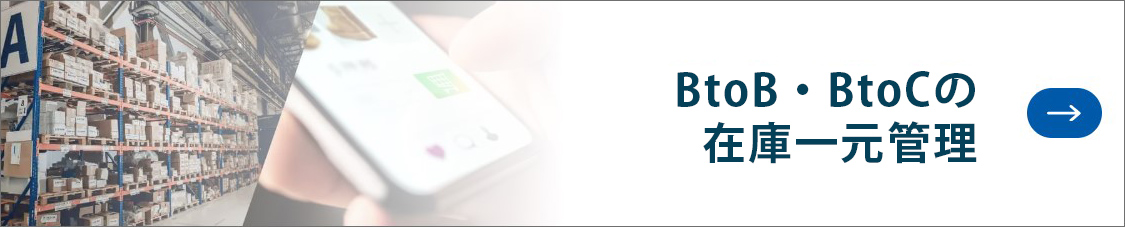