物流倉庫の現状調査を行う際のポイント
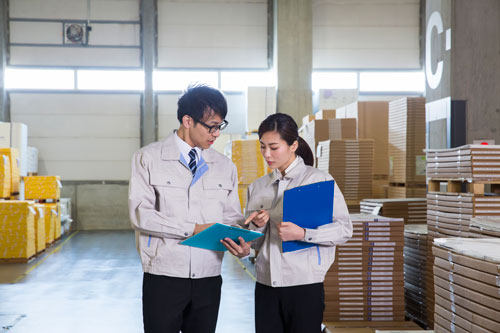
物流倉庫の業務を改善する際にまず最初に行うことが、「現状調査」です。報告書などの既存資料を確認するのももちろん大事ですが、プロジェクトメンバー自らが現場に足を運ぶ必要があります。本日は物流倉庫の現状調査をおこう上で重要なポイントをいくつか紹介させて頂きます。
目次
現状調査とは?
物流倉庫の現状調査とは「事実」を把握することにあります。何故「事実」を重要視するかというと、人によって「現状」の捉え方が変わってしまうからです。Aという作業スタッフが「これが最善の方法だ!」と思っていても、Bという作業スタッフは「今のやり方ならミスがでるかもしれない。」と感じているかもしれません。そのため、報告を上げてくる人が違えばその報告内容にもバラツキが出ます。つまり、まずはプロジェクトメンバー自らが現場に足を運び、しっかりと目で「事実」を把握し、その中でも早急に改善するべき「問題点」を洗い出す必要があります。
事実を把握するための調査
事実を把握するためには調査が必要です。調査するポイントは以下の通りです。
ーーーーーーーーーーーーーーーーーー
(When)いつ
(Who)誰が
(What)どんな仕事を
(Why)何のために
(How often)どれくらいの頻度で
(How to)どんな手順で
(Problem)どんな問題が起きているのか
ーーーーーーーーーーーーーーーーーー
例えばひとつ例にして考えてみましょう。最近、物流倉庫で事故が多発しているとします。改善プロジェクトメンバーの責務としてはすぐにでもこの問題を解決しなくてはいけません。そこで早速、現状調査を行うと次のような調査結果となりました。
ーーーーーーーーーーーーーーーーーー
(When)平成29年11月1日16時30分
(Who)山田太郎さんが
(What)商品のピッキングを
(Why)出荷作業のために
(How often)たまに
(How to)脚立を使って行っていた。
(Problem)結果、転倒してケガをした。
ーーーーーーーーーーーーーーーーーー
この調査からは色々な課題点が見えてきます。
まず1番最初に対処しないといけないのは安全を確保するということです。安全なしには物流倉庫は運営できません。脚立を使ってピッキングしているのなら、使わないというのが1番手っ取り早い安全対策です。ただ、今回の事故はそれだけが原因でしょうか?また、事故が起きたということだけが課題なのでしょうか?この調査から他のポイントについても探ってみましょう。
いつ(When)
まず「いつ(When)」というポイントに注目してみます。平成29年11月1日16時30分という調査結果がでていますが、もしかするとこの16時30分が問題であった可能性があります。運送会社の集荷が17時であった場合、16時30分にピッキングをしていては間に合う可能性が低いです。ここから考えて、もしかすると山田太郎さんは急いでいたのかもしれません。急いで作業をすると何かと問題がでます。16時30分になるまでに作業が遅れているのが把握できていたのなら、途中で人員を増やすといったことで未然に事故を防げたかもしれません。そういう意味では元々の作業に対する人員計画、作業途中のスタッフマネージメントに課題があると考えられます。
誰が(Who)
次は誰が(Who)というポイントです。今回は山田太郎さんが結果的に事故を起こしましたが、山田太郎さんが実は新人であった可能性も考えられます。新人であるが故、物流倉庫の作業ルールを知らないまま脚立を使ってしまったのかもしれません。ここから見える課題は作業員への教育体制です。例えば物流倉庫で作業する前にしっかりと安全講習を実施し、作業マニュアルを伝えていれば防げていた可能性もあります。
どれくらいの頻度で(How often)
次に注目したいのはどれくらいの頻度で(How often)というポイントです。今回はたまにという頻度でした。そこから考えると、脚立を使ってピッキングをしないといけない頻度がたまにということなので、一部の商品のみ高いところに保管されている可能性が考えられます。つまり解決策としては、高所に保管されている商品を脚立を使わなくて済む保管場所に移せば、脚立を使わずともピッキング作業ができます。そういう観点なら今回の事故は在庫管理の方法にも問題があり、今後どう保管していくかというのが課題になります。
どんな手順で(How to)
次はどんな手順で(How to)というポイントです。当然、今回の事故は脚立を使っていたことが1番大きい要因として考えられますが、もし仮にどうしても高いところにしか商品を保管するしかない場合はどうでしょうか?安全面を単に追求すると保管スペースが増えてしまったり、ピッキング作業の生産性が落ちてしまう可能性もありますので、ありとあらゆる可能性から最善な選択肢を選ぶ必要があります。その場合は脚立を使用する以外の選択肢を考える必要があります。
その1つとして考えられるのがピッキングリフトです。ピッキングリフトには作業台全周に手すりが設置されたものも存在します。厚生労働省の定める特別教育を受け、正しい使い方を行えば安全面は担保されるかもしれません。
他の方法としては物流倉庫を自動倉庫にする方法です。高い所に保管された商品でも自動倉庫なら自動でピッキングエリアに目的の商品を届けてくれます。ただ、これらマテハンの導入は投資する金額が大きいため、安全面だけではなく、費用対効果等も検討した上で導入を決定する必要があります。
まとめ
いかがでしたでしょうか?物流倉庫の現場調査もこのように要点をつかんで調査すれば、目先の問題だけではなく、ありとあらゆる課題を抽出することができます。
最後に、、、物流倉庫を運営していくという意味では危険は常に隣り合わせといってよいでしょう。例えば、ピッキングリフトを使用する場合でも、高い所に商品を保管していれば、上から商品が落ちてくる可能性もあるので、安全という意味では常に課題が残ります。導線の確保や防災訓練等、ピッキング作業のみならずトータル的に安全対策をする必要があります。
まずは自社の物流倉庫の現状を把握してみませんか?
しっかりと現状を把握して課題を解決するなら物流のコンサルタントに改善を依頼する手段もあります。
トミーズコーポレーションの物流コンサルティングサービスでは無料診断を実施しております。
まずはお気軽にお問い合わせくださいませ。
物流倉庫の現状調査ならトミーズコーポレーションの物流コンサルティングサービス
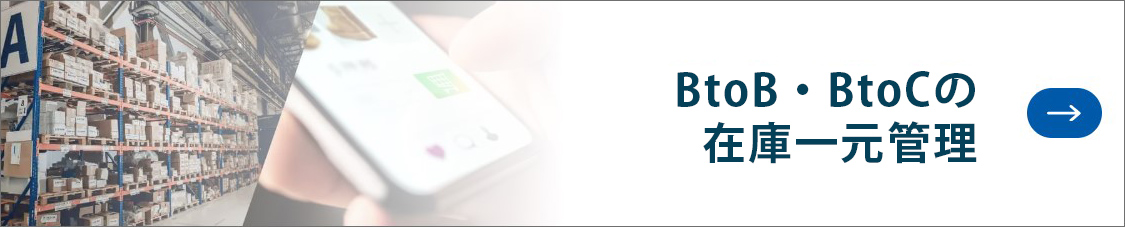