物流現場の問題点と改善・効率化について
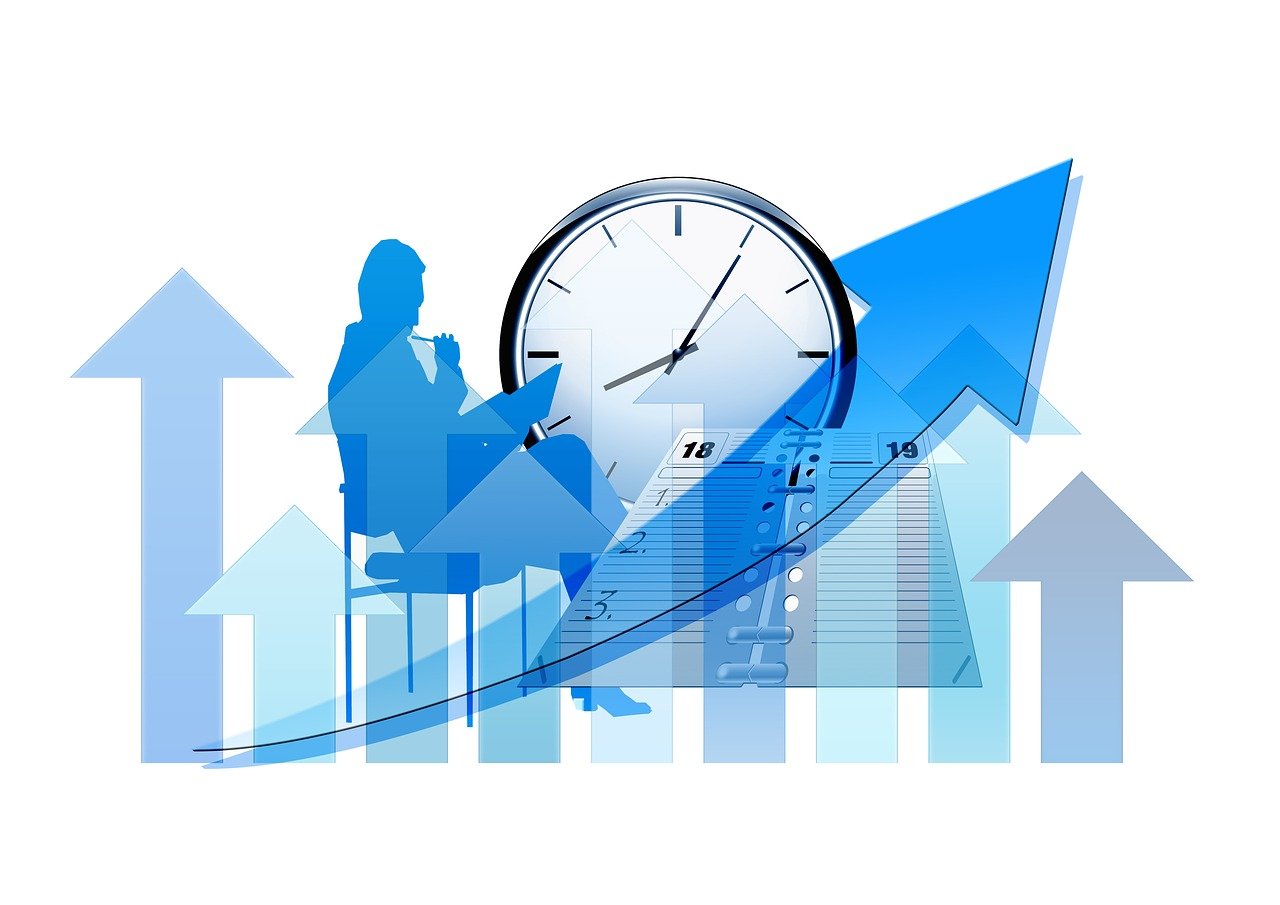
目次
はじめに
物流現場の効率化は、現代のビジネス環境で企業が競争力を維持するための重要な要素です。とりわけ「迅速で正確な配送」「コスト削減」といったニーズが高まるなか、効率化を最大化するためには、倉庫内業務にとどまらず、配送や在庫の流れ、入出荷を含めた全体の連携が欠かせません。しかし、こうした物流現場における効率化には多くの課題が残されているのが現状です。
特に、インターネット通販の拡大に伴って物流業界全体での配送量が急増し、従来の運用方法では対応が追いつかなくなっているケースも少なくありません。また、消費者の期待値も高まり「早く、確実に届けてほしい」という要望が増え、これに応えるための配送管理や効率的な輸送計画が求められるようになっています。たとえば、配送ルートを最適化したり、車両積載率を引き上げたりするなど、輸送業務においても見直しが急務です。
さらに、環境負荷の低減も効率化と並んで注目されているテーマです。配送車両からの排出ガス削減や、荷主間での共同配送を実現することにより、環境への配慮を示しつつ企業イメージの向上も図ることができます。これらの改善策を通じ、今後は、顧客満足度の向上や企業の社会的責任を果たすための取り組みが、さらに求められるでしょう。
本記事では、物流現場の効率化に向けた具体的な問題点とその改善策について詳しく解説します。配送の効率向上やコスト削減を目的としたアイデアに加え、顧客の信頼を高めるための工夫や、業界全体が注目する環境対策にも焦点を当てています。物流効率化に取り組む皆様に、ここで紹介するポイントが日々の業務改善や持続可能な物流体制の構築に役立つことを願っています。
物流現場のよくある問題点
物流現場の効率化を図る上で、業務のさまざまな段階に潜む問題点を把握することが重要です。特に近年は消費者ニーズの多様化やインターネット通販の拡大に伴い、物流現場全体での負担が増大し、多くの企業で課題が顕在化しています。ここでは、物流現場において代表的な問題点をいくつか挙げ、それぞれの影響と背景を詳しく解説します。
配送業務における問題点
配送の遅延リスクの増加
近年、配送量の増加により、従来の運用方法では配送の遅延が発生しやすくなっています。特に、繁忙期やセール時期には商品が一気に出荷されるため、通常の業務体制では対応しきれず遅れが生じやすくなります。遅延は顧客満足度を下げるだけでなく、返品やクレーム対応といった追加業務も発生させ、現場の負担がさらに増す原因にもなっています。
配送ルートの効率不足
輸送業務におけるルートが適切に最適化されていないと、無駄な走行が増え、時間や燃料の無駄が発生します。特に配達先が複数ある場合、適切なルートを設定しないと移動距離が長くなり、輸送効率が低下します。これは、燃料コストの増加だけでなく、車両や作業者の稼働効率を低下させる要因にもなります。
配送コストの増加
燃料費や車両維持費、運転手の人件費といった配送関連コストが年々上昇していることも問題です。特に、運転手の確保が難しい状況では、物流企業はコスト削減と効率化の両立が課題です。コストの増加が利益率の低下につながり、全体の物流効率にも影響を与えるため、いかに効率的に配送を行うかが大きなポイントとなっています。
倉庫内の在庫管理と連携の問題
在庫の過不足管理
倉庫内の在庫管理において、在庫の過剰や不足が頻繁に発生する場合、入出庫のタイミングや数量に問題がある可能性が考えられます。過剰在庫は倉庫スペースを圧迫し、保管コストを増加させます。一方で、在庫不足は出荷遅延や欠品を引き起こし、顧客満足度の低下に直結します。これらは、データと実際の在庫数が一致していない場合に起こりやすく、正確な管理ができていないことが背景にあるといえます。
リアルタイムな在庫情報共有の欠如
在庫情報がリアルタイムで更新されていないと、販売部門や他の拠点との情報共有がスムーズに進みません。特に、倉庫が複数ある場合、在庫状況の把握が難しく、必要な商品がどこに保管されているのか確認するのに手間がかかります。これにより、商品が必要な時にすぐに対応できず、配送や出荷のスピードが低下することがあります。
荷主や他企業との調整における問題
配送先の調整にかかる時間と手間
荷主や他企業との共同配送を行う際、配送スケジュールの調整や荷物の配分でトラブルが発生することが多く見られます。荷主ごとに異なる要求や配送時間の調整が必要になると、スケジュールの組み換えに時間を要するため、効率的に配送するのが難しくなります。また、配送先の要望に合わせたスケジュール調整は、特に繁忙期には対応が難しくなり、配送全体に遅れが発生する可能性が高まります。
異なるシステムとの連携不足
荷主や他企業とシステムを連携していない場合、情報の共有に時間がかかることがあります。たとえば、出荷情報の受け渡しや、出荷先の在庫状況の確認が手動で行われると、その都度確認作業が発生します。特に異なるシステム間でのデータの連携がうまくいっていないと、データの一貫性が保てず、作業に余分な負担がかかります。
人手不足と環境負荷に関する問題
慢性的な人手不足と従業員の負担増加
物流現場では、特にドライバー不足が深刻です。人手不足が常態化している状況では、現場で働く人の負担が増大し、長時間労働や単調な作業が疲労やモチベーションの低下を引き起こす原因になります。これにより、作業ミスが増え、全体の業務効率が低下してしまうのです。
環境負荷の増加
物流業界では、配送車両による排出ガスの問題や過剰包装による廃棄物増加など、環境負荷に対する配慮が求められています。過剰な輸送や頻繁な移動が続くと、燃料消費が増え、環境への負荷が大きくなります。また、廃棄物や包装資材の多用は、企業としての持続可能性に対する評価にも影響を与えます。
これらのように、物流現場では各段階で異なる問題が存在し、それらが全体の効率に影響を与えています。現場の課題を一つひとつ把握し、具体的な改善策を講じることで、物流業務全体のパフォーマンス向上や、コスト削減、顧客満足度の向上につなげていくことができます。
問題点の改善策
物流現場の効率化には、さまざまな段階で発生している課題に対して適切な改善策を講じることが重要です。配送業務の管理から在庫の正確な把握、共同配送や環境負荷の削減まで、物流全体でのパフォーマンスを向上させるための具体的な対策を紹介します。
配送業務における改善策
配送ルートの最適化
配送業務における効率化を図るには、まずルートの最適化が欠かせません。複数の配送先がある場合、システムによるルートの自動計算を導入することで、最も効率の良い配送順序が自動的に設定されます。これにより、走行距離や時間が短縮され、燃料コストの削減と共に作業者の負担も軽減されます。また、配送ルートをリアルタイムで調整する機能があると、渋滞などの突発的な状況に応じて効率的にルートを変更でき、配送遅延を防ぐことが可能です。
配送車両の積載率向上
効率的な配送のためには、配送車両の積載率を高めることが有効です。複数の荷主からの荷物をまとめて配送する「コンソリデーション」の仕組みを活用し、トラックの積載率を向上させることで、配送回数を減らすことができます。これにより、燃料や人件費などのコスト削減が実現するほか、環境負荷も軽減されます。特に定期便の場合、毎回の積載率をチェックし、積載が少ない場合には荷主と調整を図り、効率的な輸送が実現するようにしましょう。
配送進捗のリアルタイム管理
顧客が配送状況を把握できるように、リアルタイムでの配送追跡システムを導入することで、配送の進捗が簡単に確認できるようになります。顧客側が追跡情報を確認できると、配送遅延や到着予定に関する問い合わせが減り、顧客満足度の向上が期待できます。また、配送現場でも進捗状況が把握できるため、トラブル発生時の対応が迅速に行え、現場全体の作業効率が向上します。
在庫管理と情報共有の改善策
在庫の可視化と自動管理システムの導入
正確な在庫管理には、倉庫内にある在庫の「可視化」が重要です。RFIDやバーコードを用いた自動管理システムを導入することで、リアルタイムに在庫の数や保管場所が把握でき、誤出荷や欠品を防ぐことができます。システム上で在庫数が即時更新されるため、他部門との情報共有もスムーズに進み、物流現場全体の効率化につながります。
需要予測に基づいた在庫補充の調整
過剰在庫や欠品を防ぐためには、過去の販売データや需要予測を基にした在庫管理が効果的です。AIやビッグデータ分析を活用して、需要の変動に応じた在庫補充ができるように調整することで、在庫数を最適化し、保管コストを抑えられます。特に、季節ごとに販売が増減する商品や、セール時に需要が急増する商品の補充計画を立てることが、在庫管理の改善に役立ちます。
在庫情報のリアルタイム共有
複数の拠点や販売チャネルがある場合、在庫情報をリアルタイムで共有するシステムが不可欠です。各拠点で在庫数や商品状況が把握できると、必要な商品の調達や移送が効率的に行われます。これにより、欠品による販売機会の損失を防ぎ、顧客ニーズに応えるための柔軟な対応が可能です。特に緊急の受注時には、各拠点の在庫状況が即座に確認できるため、スピーディな対応が実現します。
荷主や他企業との調整における改善策
共同配送スケジュールの最適化
荷主間での共同配送を行う際には、配送スケジュールを効率的に管理することが重要です。各荷主の要望を統一のスケジュールにまとめることで、無駄な配送やスケジュールの変更が減り、現場での対応も楽になります。また、配送ルートや時間帯を共有することで、各企業のリソースを効率的に活用することができ、トラックの積載効率が向上し、物流コストの削減が実現します。
システム連携によるデータ共有の自動化
荷主や他企業と連携する場合、異なるシステム同士が円滑にデータを共有できるよう、APIなどを活用してシステムを連携させることが有効です。出荷情報や配送先の在庫情報が自動でシステム間に反映されると、手動での入力が減少し、ヒューマンエラーも防ぐことができます。また、情報の一貫性が保たれ、荷主や配送業者の間でスムーズに情報が共有されるため、物流業務の全体効率が向上します。
人手不足と環境負荷への対応策
自動化技術の導入と業務負担の軽減
物流業界での人手不足の問題は、自動化技術によってある程度解消できます。例えば、ピッキングや積み込みの自動化、無人搬送車(AGV)の導入により、倉庫内作業の負担が大幅に軽減されます。また、配送業務では、自動運転車両やドローンを活用した配送方法が実験的に導入されており、今後さらなる効率化が期待されています。こうした自動化技術の活用により、限られた人員で物流のスムーズな運営が可能になります。
労働環境の改善とスタッフ教育
作業効率を高めるだけでなく、作業環境の整備やスタッフ教育も人手不足の解消に役立ちます。物流現場で働くスタッフに対して、スキルアップ研修や効率的な作業手順の指導を行うことで、作業精度が向上し、現場の負担が軽減されます。また、定期的な休憩や労働環境の見直しを行い、作業者の健康維持をサポートすることで、離職率の低下にもつながり、安定した労働力を確保することができます。
環境負荷を抑えるエコ物流の推進
物流業界では、配送車両からの排出ガス削減や、過剰包装の見直しなどを通じて、環境負荷を抑える「エコ物流」が求められています。配送車両には、燃費効率の良い車両や電気自動車を採用し、排出ガスを抑えることが可能です。また、配送頻度の調整や共同配送を行うことで、走行距離を削減し、燃料消費を抑えることができます。加えて、再利用可能な梱包材の導入や過剰包装の削減を行うことで、廃棄物を減らし、環境への配慮を強化することができます。
これらの改善策を通じて、物流現場での課題解消が進み、配送効率の向上やコスト削減、環境負荷の軽減といったさまざまな効果が期待できます。物流業務全体のパフォーマンス向上と顧客満足度の向上に貢献するために、現場での実現可能な改善策を一つひとつ取り入れていくことが重要です。
物流現場の効率化するためには
物流現場を効率化するためには、個々の業務改善だけでなく、全体を俯瞰した戦略的な取り組みが重要です。ここでは、物流現場全体の効率化を進めるために取り組むべき具体的なポイントについて解説します。これらは、コスト削減、作業負担の軽減、そしてサービス品質向上に役立つものです。
配送の効率化を図る
AIを活用した配送ルートの最適化が効果的です
配送業務の効率化には、AIを活用したルートの最適化が非常に有効です。AIを使うことで渋滞情報や配送順を加味し、リアルタイムで最も効率的なルートを自動的に計算でき、無駄な走行が削減されます。これにより、配送時間や燃料コストを抑え、配送遅延のリスクも軽減可能です。複数の配達先があるルートでは、AIが最短経路を選定してくれるため、配送効率が向上します。
配送拠点を見直し、効率化を図る
配送拠点を戦略的に再配置することで、効率化が進みます。需要が集中しているエリアに小型の配送拠点を設けることで、顧客に近い場所からの出荷が可能になり、配送時間が短縮されます。さらに、拠点間で在庫情報や出荷状況を共有することで、拠点間の連携が強まり、効率的な配送体制が整います。
在庫管理とシステム導入を進める
倉庫内のロケーション管理システムが鍵となります
在庫管理の効率化を図るためには、倉庫内でのロケーション管理が欠かせません。バーコードやRFIDによって在庫の保管場所をシステム化すると、ピッキング作業や商品検索がスムーズに進みます。さらに、在庫移動もリアルタイムで把握できるため、正確な在庫管理が実現し、欠品や過剰在庫のリスクが抑えられます。
自動倉庫や無人搬送車(AGV)を導入し、作業の効率化を図る
自動倉庫システムや無人搬送車の導入は、倉庫業務のスピードと効率を大きく向上させます。自動倉庫では商品の入出庫がシステムで自動管理され、作業者によるミスが減少します。無人搬送車を使えば、作業者の負担が軽減され、効率的に在庫が移動できるようになります。特に大規模な倉庫では、自動化によって作業負担が軽減し、効率的な物流管理が可能です。
需要予測を取り入れた在庫補充を行う
在庫管理の精度を向上させるためには、AIによる需要予測を活用した在庫補充が効果的です。これにより、需要変動に合わせた在庫確保が可能になり、過剰在庫や欠品を抑えられます。たとえば、季節商品の需要増加やセール時の販売数を予測し、それに合わせた補充を行うことで、保管スペースの有効活用と在庫コストの削減が実現します。
コスト削減と環境配慮を実現するためには
配送車両の積載率を高め、共同配送を促進します
配送効率を高め、コストを削減するためには、配送車両の積載効率を意識することが重要です。複数の荷主が共同で荷物を積載する「共同配送」を採用することで、配送回数が減り、車両の稼働効率が向上します。また、荷主と配送スケジュールを調整し、積載量を増やすことで、燃料費や人件費が抑えられ、CO2排出量の削減にもつながります。
リサイクル可能な梱包資材を活用し、環境負荷を軽減
物流現場の持続可能性を高めるためには、環境配慮型の梱包資材の活用が重要です。リサイクル可能な素材を使った梱包材や、再利用可能な梱包方法を導入することで、廃棄物の削減が実現します。環境にやさしい梱包材を採用することで、企業の環境配慮への姿勢を示し、企業イメージの向上にもつながります。
燃料効率の良い車両や電動車両への切り替え
環境負荷とコスト削減の両面で効果的な対策として、燃費の良い車両や電動車両の導入が挙げられます。燃費効率が高い車両を使うことで、燃料費とCO2排出量が削減できます。また、電動車両を取り入れることで、配送業務における環境負荷の低減が期待でき、環境配慮型の運用が可能になります。
労働力確保と教育体制を整えるためには
作業手順の標準化とマニュアル整備
物流現場の効率化には、作業手順を標準化し、マニュアルを整備することが大切です。各作業の標準化とマニュアル化により、新しいスタッフがスムーズに業務に取り組むことができ、属人化を防げます。マニュアルが整備されることで、繁忙期や急な人手不足の際も円滑に作業が進められます。
作業者のスキルアップとモチベーション向上に注力
作業効率を高めるには、作業者のスキルとモチベーションの維持が重要です。スタッフ教育や定期的なスキル研修を実施することで、作業者の成長をサポートし、現場でのミスを減らすことができます。また、作業環境の改善やモチベーション向上策を取り入れることで、作業者の離職率が低下し、安定した労働力を確保しやすくなります。
最新技術を活用して効率化を図る
IoTを活用し、設備や在庫を一元管理します
物流現場での効率化には、IoTを用いて在庫や設備をリアルタイムで監視・管理することが効果的です。たとえば、倉庫内の温湿度管理や機器のメンテナンスをIoTで行うことで、商品品質の維持や設備の効率的な稼働が可能になります。また、IoTと自動化技術を組み合わせて稼働率を最適化することで、物流全体の効率が向上します。
AIを活用して需要予測と在庫管理を最適化
AIを使った需要予測システムにより、消費者の動向や季節性のある変動を正確に把握し、それに応じた在庫管理が可能です。これにより、無駄な在庫を減らし、欠品のリスクを防ぎます。需要予測の導入によって、倉庫スペースを有効活用し、在庫コスト削減にもつながります。
物流現場での効率化を実現するためには、配送から在庫管理、環境配慮、労働力確保、最新技術の導入まで幅広い取り組みが必要です。これらの施策を通じて、物流全体でのパフォーマンス向上やコスト削減、サービス品質の向上が期待できます。
まとめ
物流現場の効率化は、企業の競争力を高め、顧客満足度を向上させるために不可欠な要素です。本記事で紹介したように、物流業務の各段階で発生する課題に対して適切な改善策を講じることで、業務全体のパフォーマンスが向上します。
まず、配送業務では、AIによるルート最適化や車両の積載効率の向上、リアルタイム追跡システムの導入により、コスト削減と配送のスピード向上を実現できます。また、倉庫内では、在庫管理の精度を高めるための自動化システムやロケーション管理の導入が、在庫の可視化や誤出荷防止に役立ち、無駄な時間を削減します。
さらに、環境への配慮も物流の重要なテーマです。燃料効率の良い車両や電動車両の導入、再利用可能な梱包資材の使用など、エコ物流の推進により、持続可能な物流体制の構築が可能になります。そして、人材確保と作業者の教育も欠かせない要素であり、作業の標準化やマニュアル整備、スキルアップ研修を通じて現場の安定した労働力を支え、効率化を推進する基盤が整います。
物流現場の改善は、単に作業効率を高めるだけでなく、コスト削減や顧客満足度の向上にもつながります。弊社トミーズコーポレーションでは、これまでに培ったノウハウを活かし、アパレル物流を中心に様々な業界のお客様の物流改善を支援してまいりました。物流現場の改善に関するご相談は、お気軽にお問い合わせください。
トミーズコーポレーションの入荷保管についてはこちらから
トミーズコーポレーションの物流システムについてはこちらから
流通加工における格安の段ボールならトミーズ
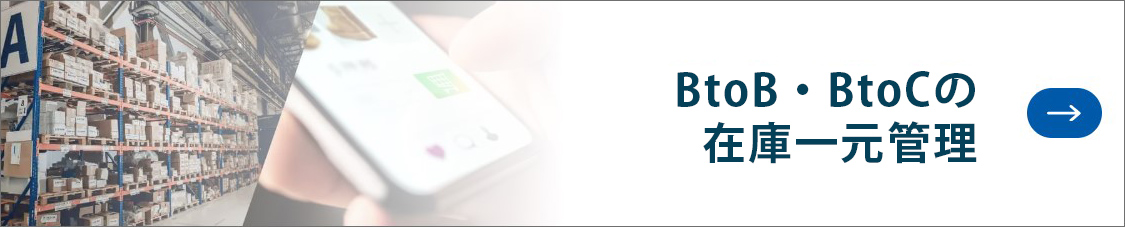